Noticias
Pocas veces la industria automotriz ha hecho esperar tanto tiempo para entregar un automóvil o un camión a quien ya le ha pagado, pero a partir de la pandemia de Covid-19 la industria ha enfrentado una sequía en la producción y esta vez ha sido superada por la demanda.
De acuerdo con los especialistas, la sequía en la producción de automóviles y camiones pesados es causada por la falta de chips o semiconductores, así como por la falta de contenedores para el transporte, lo que provoca que las principales armadoras, tanto de vehículos ligeros como pesados, dejen a sus compradores en listas de espera.
Lea también: Sector automotriz, retos y oportunidades ante el T-MEC
Guido Vildozo, Senior Manager, Americas Light Vehicle Sales Forecasting de IHS Markit, comentó que el impacto de semiconductores va a estar en la industria un buen tiempo y no anticipan ningún tipo de normalización hasta 2023.
“La mayor limitante de ventas que vamos a tener durante el próximo año y medio es la disponibilidad de producto, que dependerá del comportamiento de semiconductores en el mercado global”, expuso el directivo, ante lo cual estimó que en el mexicano se tiene posibilidades de quedar por debajo del millón de unidades en la comercialización de vehículos ligeros.
Para el especialista, el golpe que significa la falta de semiconductores a nivel global equivale a la producción de 40 plantas y se va a extender a lo largo de 2022. La capacidad de producción al día está un 20% por debajo de donde está la demanda en este ciclo de recuperación que se vive en el entorno global y la industria estará entrando en una política de normalización en la producción hacia 2023.
Ante esta crisis por la falta de semiconductores, Fausto Cuevas, director general de la Asociación Mexicana de la Industria Automotriz (AMIA) estimó que la producción de vehículos ligeros para este año se ubicará entre 4 y 5% por debajo de los niveles de producción del año pasado, cuando alcanzaron 3 millones 40 mil 178 unidades.
Alberto Bustamante, director de Comercio de Industria Nacional de Autopartes (INA), estimó que en el mercado mexicano, para este año, se podrían dejar de producir entre 550 mil y 600 mil unidades por la falta de semiconductores; en tanto que en toda la zona de Norteamérica se dejarán de producir entre 2 millones 800 mil y 2 millones 900 mil vehículos por esta razón.
Costos logísticos y de manufactura
A la falta de chips para la industria automotriz se sumó la falta de contenedores a nivel global, lo que es un problema de logística que impacta a la proveeduría y a la producción.
Estos factores crearon la “tormenta perfecta” para el retraso en la entrega de las unidades ya vendidas, si alguien compra un vehículo nuevo ahora tendrá su unidad hasta 2022, comentó Miguel Elizalde, presidente de la Asociación Nacional de Productores de Autobuses Camiones y Tractocamiones (ANPACT).
Masatomo Kumabe, presidente y director general de Hino Motor Sales México, expresó que esta falta de contenedores para la importación y exportación de mercancías afectó a la empresa que importa a través del Puerto de Lázaro Cárdenas, Michoacán, las piezas de ensamble en la planta de Silao, Guanajuato.
Estimó que la escasez de contendores se mantendrá hasta 2022, por lo que se requiere de alta eficiencia y planeación con los concesionarios para coordinar la entrega a sus clientes; aun así mantiene la expectativa de colocar 3 mil unidades en el mercado mexicano y llegar a una capacidad máxima de producción de 2 mil 400 unidades para cubrir la demanda del mercado nacional.
Además del incremento en los costos de la logística de los contenedores, Armando Soto, presidente de la consultora Kaso y Asociados, expresó que la industria se enfrenta al reto de contener las presiones inflacionarias derivadas de aumentos de precios de las materias primas y de la logística.
En estos últimos meses, se han visto aumentos muy importantes en los precios de las materias primas y en la logística del sector, sobre todo en las principales materias primas que se utilizan en la fabricación de vehículos nuevos como efectos de los desequilibrios en la producción y logística de distribución.
“Estas disrupciones se generaron en la cadena de suministro en varios sectores cuando se comenzó a dar la apertura, esto aceleró la demanda por materias primas y componentes a una velocidad que excedió las posibilidades de abastecimiento que se tenían en esos momentos y empezaron a crecer los precios de manera exorbitante”, explicó Armando Soto.
Destacó que en el caso de las materias primas para el sector, de febrero de 2020 —mes en que empezó a arreciar la pandemia— a septiembre de 2021, el acero laminado tuvo un incremento en sus precios internacionales del 156%, el mineral de hierro 30%, el aluminio 68%, y el petróleo 41%; este incremento a su vez tuvo impactos en plástico y resinas automotrices con incrementos de 40 por ciento.
Se ha discutido si este es un efecto transitorio y conforme se vaya avanzando en la apertura de las economías va a moderarse y a desaparecer, pero la realidad es que el proceso de vacunación no ha sido parejo en el mundo y muchos países que son proveedores de estas materias primas van muy atrasados, agregó Armando Soto.
Se vuelve crucial saber si esto se va a traducir completamente en los precios de las unidades, ya que se están experimentando costos de logística siete veces altos, en el traslado de un contenedor comparado con los precios que existían antes de la pandemia, además el costo del personal se ha incrementado de manera importante y “toda esa esfera que se está gestando no está teniendo salida y cuando tiene salida, los que pagan son los consumidores”.
Otras noticias de interés
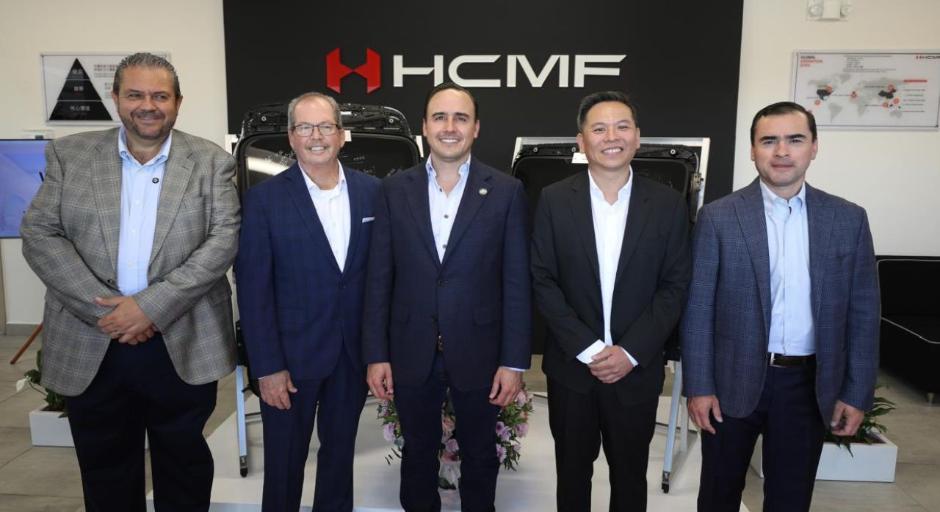
Inicia operación nueva planta de autopartes
La empresa HCMF concretó la apertura de una nueva planta de autopartes
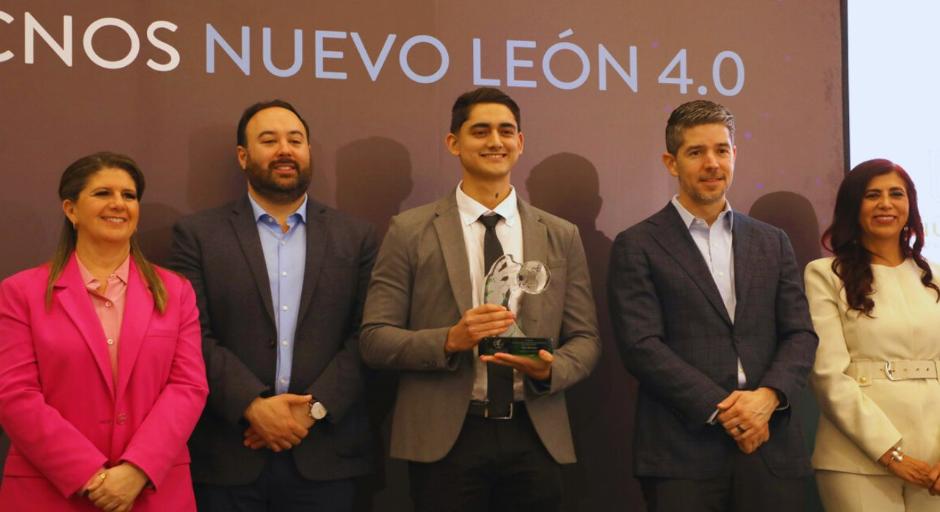
Gana Kia México premio de calidad
La planta de Kia México en Pesquería, Nuevo León, fue reconocida por

Se registra ligera alza económica
El Indicador Oportuno de la Actividad Económica (IOAE) estimado por el INEGI
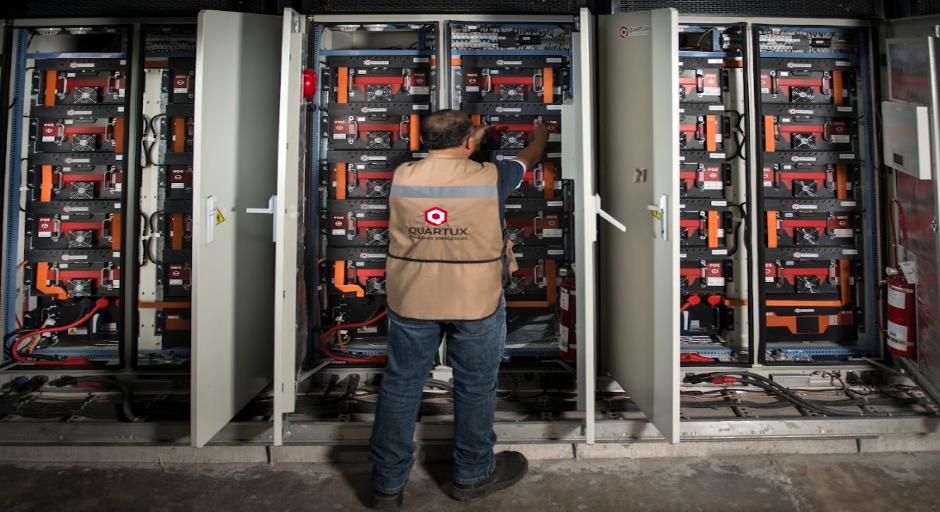
Imperante la modernización de la red eléctrica mexicana
La digitalización en México avanza a un ritmo superior al de la
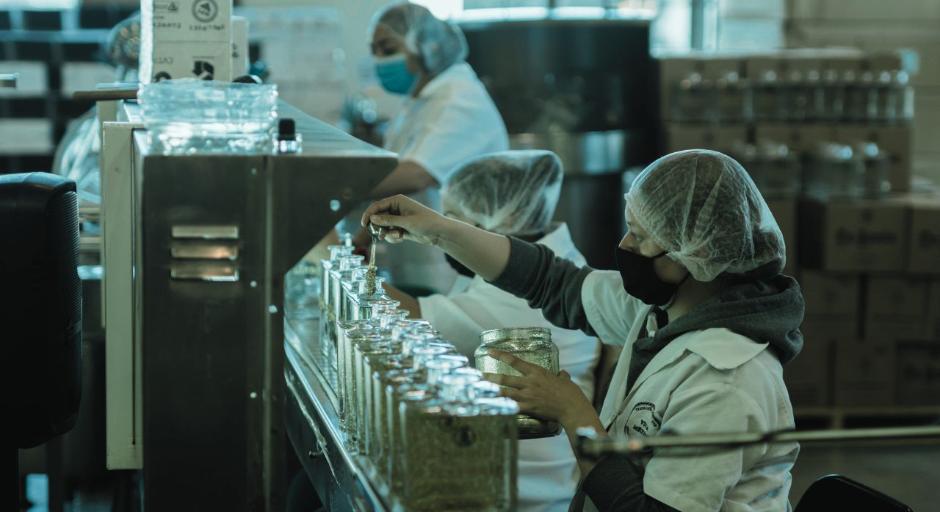
Reporta IMMEX caída en personal ocupado
En junio de 2025, el Programa de la Industria Manufacturera, Maquiladora y
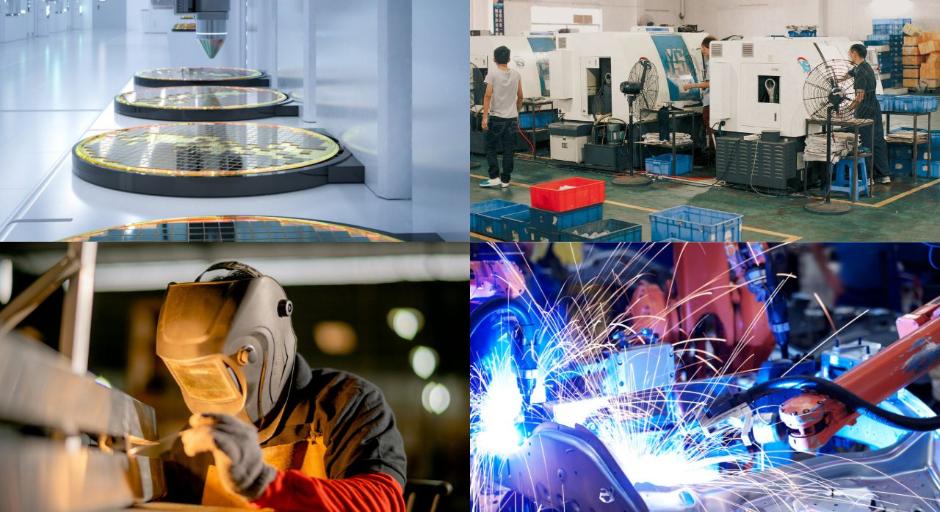
Fomentan competitividad industrial en Querétaro
El lanzamiento del Centro de Competitividad de la Industria (CCI) en Querétaro